電線電纜生產(chǎn)線上,兩道相似的工序設備常讓從業(yè)者產(chǎn)生混淆——束絲機與絞線機究竟有何不同? 在導體加工領域,這兩種設備雖同屬線材成型機械,卻在工藝原理、結構設計和應用場景上存在本質差異。理解這些區(qū)別不僅能幫助企業(yè)精準選型,更能優(yōu)化線纜產(chǎn)品的機械性能和導電特性。
一、結構原理的本質分野
束絲機的核心功能在于實現(xiàn)多根單絲的同心絞合。其通過精密張力控制系統(tǒng),將6-60根直徑0.08-2.6mm的銅、鋁單線按同心圓分層排列,每層絞向相反。典型設備采用雙節(jié)距絞合技術,保證絞合節(jié)距穩(wěn)定在80-120倍線徑范圍,這種結構使導體截面積最大化,特別適用于需要高載流量的電力電纜制造。
絞線機則專攻螺旋絞合工藝,其核心在于分線盤的動態(tài)補償設計。設備通過行星輪系驅動線盤公轉與自轉,實現(xiàn)7-37根導體的螺旋纏繞。獨特的預扭裝置能消除導體殘余應力,絞合節(jié)距通??刂圃?2-20倍線徑,這種緊密結構賦予線材優(yōu)異的柔韌性和抗彎曲疲勞特性,在移動設備用線纜領域具有不可替代性。
二、加工對象的顯著差異
從材料適配性來看,束絲機主要處理退火軟態(tài)導體。以35kV中壓電纜為例,要求導體延伸率≥25%,束絲工藝能完美保持單絲塑性變形能力。而絞線機更擅長加工半硬態(tài)導體,如通信電纜用磷青銅線,其抗拉強度需達到450-750MPa,螺旋絞合產(chǎn)生的預應力可提升線材整體強度。
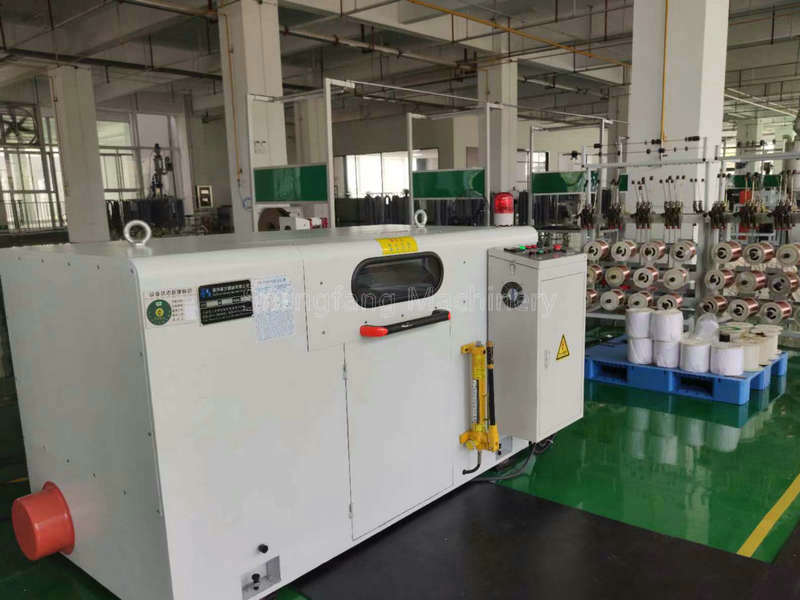
在導體規(guī)格方面,束絲機最大加工截面可達2500mm2,滿足特高壓輸電需求;絞線機則精于微細線加工,0.016mm超細合金線的絞合精度可達±0.003mm,這對5G通信線纜的趨膚效應控制至關重要。某知名線纜企業(yè)的測試數(shù)據(jù)顯示:相同截面積下,絞線工藝使高頻信號傳輸損耗降低18%-22%。
三、工藝參數(shù)的對比分析
*速度參數(shù)*呈現(xiàn)明顯分野:束絲機最高轉速通常不超過1500rpm,重點保證絞合同心度;而高速絞線機可達4500rpm,配合恒張力收線系統(tǒng),生產(chǎn)效率提升3-5倍。但需注意,當線徑超過1.2mm時,絞線機的優(yōu)勢區(qū)間會急劇收窄。
*精度控制*方面,現(xiàn)代束絲機配置激光測徑儀+CCD視覺系統(tǒng),直徑公差控制在±0.5%;絞線機則依賴多軸伺服聯(lián)動,節(jié)距波動率≤1.2%。某德系設備廠商的實測數(shù)據(jù)表明:在0.5mm線徑加工中,絞線機的橢圓度比束絲工藝降低40%。
四、應用場景的精準劃分
電力傳輸領域是束絲機的主戰(zhàn)場。500kV超高壓電纜要求導體圓整度>98%,束絲工藝形成的致密結構能將交流電阻降低15%-20%。反觀絞線機在柔性應用場景更具優(yōu)勢:機器人關節(jié)線纜經(jīng)過36次絞合后,彎曲壽命從5萬次提升至50萬次,這是傳統(tǒng)束絲工藝無法實現(xiàn)的。
新興領域的需求差異更明顯:新能源汽車高壓線束要求導體耐溫200℃+,束絲機的分層絕緣技術可集成耐高溫涂層;而智能穿戴設備的0.1mm直徑導線,必須通過絞線工藝實現(xiàn)5%以下的伸長率,確保萬次彎折不斷芯。
五、設備配置的關鍵區(qū)別
從傳動系統(tǒng)看,束絲機多采用齒輪變速箱+電磁離合器,保證低速大扭矩輸出;絞線機則標配伺服電機+諧波減速器,實現(xiàn)0.1°級別的轉角精度。某日系設備廠商的對比試驗顯示:在0.08mm線徑加工中,伺服系統(tǒng)使斷線率從1.2%降至0.03%。
輔助裝置配置差異更大:束絲機必須配備在線退火裝置,即時消除加工硬化;絞線機則集成渦流檢測儀,實時監(jiān)控導體缺陷。值得關注的是,智能化升級趨勢下,新一代設備開始融合兩種工藝優(yōu)勢——某國產(chǎn)創(chuàng)新機型通過模塊化設計,實現(xiàn)束絞工藝的智能切換,轉換時間縮短至15分鐘。
線纜工程師的選型決策,本質上是對產(chǎn)品性能與成本效益的平衡。當需要*大截面、高載流*特性時,束絲機是不二之選;而追求*高柔性、精密傳輸*的應用場景,絞線機展現(xiàn)獨特優(yōu)勢。隨著復合導體材料的普及,兩種設備的工藝邊界正在模糊,但對核心差異的透徹理解,始終是做出正確技術決策的前提。
TAG: